Finally finished my complete restoration of this piece and its case and wanted to share my process for folks wanting to try doing more amber repair too!
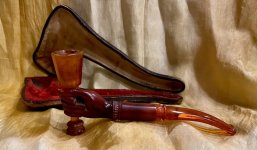
vs before
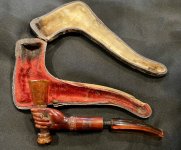
My husband bought this pipe for me as a project as I have been having fun realigning and repairing stripped or broken amber stems and other various fixes on his pipes over the last year. I posted in my introduction post with the first half of this project (digging out half a container of superglue and a toothpick from an old repair that held the cup on, re-drilling the hole, using amber chips, files, and superglue to recreate the missing parts of the bead at the base of the cup, and getting the amber cup glued in and fully sealed and airtight), but it was still missing a large amber piece between the meerschaum and the stem which required buying some raw amber in the correct color and waiting for it to arrive. There was a substantial difference in the size of the two pipe pieces and the case showed what appeared to be space for a larger bead that had once separated them.
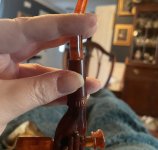
I had never seen a pipe like this before with amber attached to the bowl, but my husband later found another in an old private auction which appeared to be the same make, which gave me an idea of the intended size and shape, even if it was partially hidden by the pipe stand (photo from Piguet Auction House).
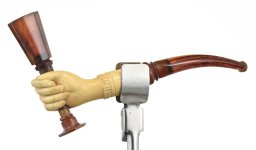
(also showed me exactly how much of the cup stem was lost before I got it!)
Jeweler's saw, files, and sandpaper can work wonders on amber! This was my first attempt at true carving instead of just repairing small sections, but it was faster than I expected. I used a drill bit manually for the central hole then used pencil to mark my guide shapes.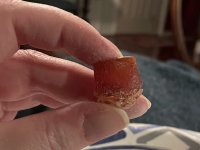
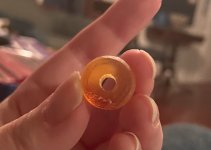
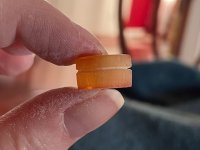
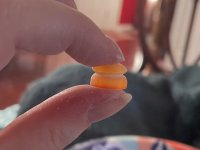
With the bead set and polished I could finally start putting it together!
I had already removed the old, broken bone tenon that had been glued back together by using nail polish remover (this is a strong solvent for superglue and many other glues, but can make newer amber slightly foggy and require a polish after, but well worth it to me to reduce the risk of the amber shattering when trying to remove the old tenon). I've tried a few replacement tenon options but I have had by far the best experiences purchasing vintage unused bone tenons from online. A gentle scraping and cleaning of the amber threads and a very light sanding of the tenon and I was able to make an option from my existing stash work!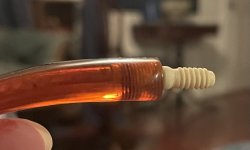
A little bit of manual drilling plus wood glue and paper to make supports in the meerschaum and the tenon and newly polished bead could be glued in!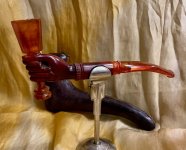
On gluing amber: I have found amber to take superglue incredibly well, but it does require some mild prep and technique. If there is any nicotine or tar on the surface it won’t hold and will just be a mess, also if you use too much it will both drip/run where it shouldn't be and also not hold and is likely to slip because it can't bond fast enough. If working with a clean surface (I always wipe down thoroughly with alcohol and make sure there is no visible residue then let fully dry) only a very very thin layer of glue is needed to hold properly, far less than could clog the hole. This has the double advantage of curing faster and without slipping on the extra glue, and meaning I don't have to worry about drips sealing the hole and therefore not needing to use a greased pipe cleaner as a protector (which if any of the vaseline gets onto the amber surface when you put it in it will stop the glue from setting properly, just like any oily residue). If you need to fill a larger gap they do make gel superglue instead of liquid which is thicker and will not run, again meaning no need to worry about drips/spills. A quick hit with a clean pipe cleaner with a small bit of nail polish remover on it can be passed through if you're worried though. Being certain my glue was staying where I put it, far away from the stem side, also means much easier time for alignment - can just screw the tenon into the stem, apply your small amount of glue on the lower half of the tenon so it doesn't push up into the stem area, then fit everything into place and let set knowing the alignment is exactly what you want it to be! Then just unscrew the stem when set and it's good!
All that was left then was cleaning the case. It was an absolute mess visually, but pretty quick to fix. A quick sanding off the rust from the hinge that had seized (and presumably torn out the missing chunk of the case), wiggling then using pliers to get the pin properly set on the bowl-side, then reattaching the now non-rusty hinge, and it was functional at least, even if it looked a mess. Dissolving the caked-on gunk on the velvet and satin was a bit more of a project, but alcohol and dish soap is a wonderful combo with smoking-related stains, and over the course of 3 paper towels I was able to lift the majority of it all then let it dry out overnight. Wood glue is my preferred option for wood/leather/fabric and applying it with a pin dipped in the glue gives a ton of control, letting me work the fabric, board, and bits of leather back into place.
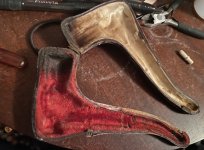
to
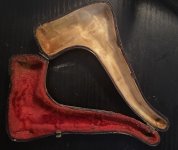
Overall this was an incredibly fun project! While my husband is the smoker, not me (though he did take the lovely photos for me!) I may need to figure out how to smoke a cheroot just to give this pipe a try now that it’s fully working again! If folks have questions about the process feel free to ask - I'm a teacher and love sharing ideas and tips!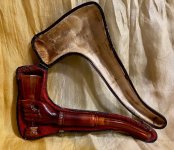
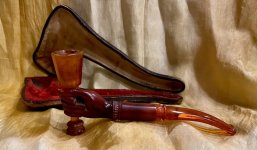
vs before
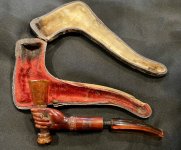
My husband bought this pipe for me as a project as I have been having fun realigning and repairing stripped or broken amber stems and other various fixes on his pipes over the last year. I posted in my introduction post with the first half of this project (digging out half a container of superglue and a toothpick from an old repair that held the cup on, re-drilling the hole, using amber chips, files, and superglue to recreate the missing parts of the bead at the base of the cup, and getting the amber cup glued in and fully sealed and airtight), but it was still missing a large amber piece between the meerschaum and the stem which required buying some raw amber in the correct color and waiting for it to arrive. There was a substantial difference in the size of the two pipe pieces and the case showed what appeared to be space for a larger bead that had once separated them.
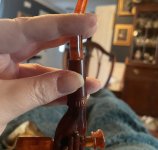
I had never seen a pipe like this before with amber attached to the bowl, but my husband later found another in an old private auction which appeared to be the same make, which gave me an idea of the intended size and shape, even if it was partially hidden by the pipe stand (photo from Piguet Auction House).
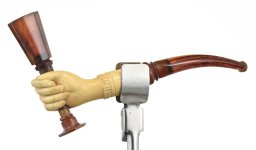
(also showed me exactly how much of the cup stem was lost before I got it!)
Jeweler's saw, files, and sandpaper can work wonders on amber! This was my first attempt at true carving instead of just repairing small sections, but it was faster than I expected. I used a drill bit manually for the central hole then used pencil to mark my guide shapes.
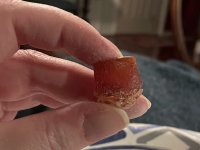
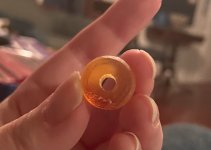
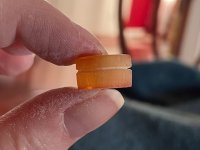
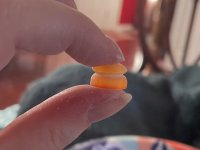
With the bead set and polished I could finally start putting it together!
I had already removed the old, broken bone tenon that had been glued back together by using nail polish remover (this is a strong solvent for superglue and many other glues, but can make newer amber slightly foggy and require a polish after, but well worth it to me to reduce the risk of the amber shattering when trying to remove the old tenon). I've tried a few replacement tenon options but I have had by far the best experiences purchasing vintage unused bone tenons from online. A gentle scraping and cleaning of the amber threads and a very light sanding of the tenon and I was able to make an option from my existing stash work!
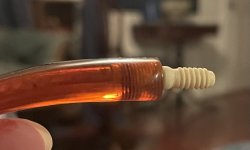
A little bit of manual drilling plus wood glue and paper to make supports in the meerschaum and the tenon and newly polished bead could be glued in!
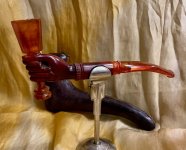
On gluing amber: I have found amber to take superglue incredibly well, but it does require some mild prep and technique. If there is any nicotine or tar on the surface it won’t hold and will just be a mess, also if you use too much it will both drip/run where it shouldn't be and also not hold and is likely to slip because it can't bond fast enough. If working with a clean surface (I always wipe down thoroughly with alcohol and make sure there is no visible residue then let fully dry) only a very very thin layer of glue is needed to hold properly, far less than could clog the hole. This has the double advantage of curing faster and without slipping on the extra glue, and meaning I don't have to worry about drips sealing the hole and therefore not needing to use a greased pipe cleaner as a protector (which if any of the vaseline gets onto the amber surface when you put it in it will stop the glue from setting properly, just like any oily residue). If you need to fill a larger gap they do make gel superglue instead of liquid which is thicker and will not run, again meaning no need to worry about drips/spills. A quick hit with a clean pipe cleaner with a small bit of nail polish remover on it can be passed through if you're worried though. Being certain my glue was staying where I put it, far away from the stem side, also means much easier time for alignment - can just screw the tenon into the stem, apply your small amount of glue on the lower half of the tenon so it doesn't push up into the stem area, then fit everything into place and let set knowing the alignment is exactly what you want it to be! Then just unscrew the stem when set and it's good!
All that was left then was cleaning the case. It was an absolute mess visually, but pretty quick to fix. A quick sanding off the rust from the hinge that had seized (and presumably torn out the missing chunk of the case), wiggling then using pliers to get the pin properly set on the bowl-side, then reattaching the now non-rusty hinge, and it was functional at least, even if it looked a mess. Dissolving the caked-on gunk on the velvet and satin was a bit more of a project, but alcohol and dish soap is a wonderful combo with smoking-related stains, and over the course of 3 paper towels I was able to lift the majority of it all then let it dry out overnight. Wood glue is my preferred option for wood/leather/fabric and applying it with a pin dipped in the glue gives a ton of control, letting me work the fabric, board, and bits of leather back into place.
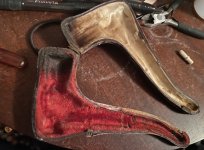
to
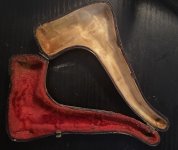
Overall this was an incredibly fun project! While my husband is the smoker, not me (though he did take the lovely photos for me!) I may need to figure out how to smoke a cheroot just to give this pipe a try now that it’s fully working again! If folks have questions about the process feel free to ask - I'm a teacher and love sharing ideas and tips!
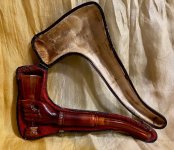