I finished this one a few weeks back, before I got sick, and just got busy prepping for art show season. This was just for me, and to play with an idea that I had. Bird enthusiasts may know cuttlebone as those things that can be gotten from pet stores to give their beloved birds a bit of calcium or to sharpen their beaks, or whatever birds get from these things.
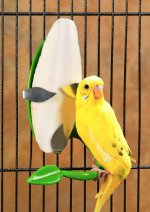
But, it is also a part of an ancient jewelry/metalsmithing process known as cuttlebone casting. There are refences to it's use in Norman and even Danish (or Northernmen) jewelry. It is very similar to casting used by Pre-Columbian sandstone processes, where the design is scratched into the soft material and then the molten metal is poured into the primitive mold. Cuttlebone has these ridges that make for a unique design on the finished piece. You cannot completely control how the finished piece will come out, so it is a bit serendipitous, or a balance between control and natural consequence.
I have made hundreds of rings using this process, and it is always a surprise how they turn out. I do have somewhat of an idea of how these will turn out, but the resulting ridges are hit or miss. But, I make a trench into the bone from the cuttlefish and then put two together to make a mold, and then pour the metal into the mold using merely gravity to fill the recesses.
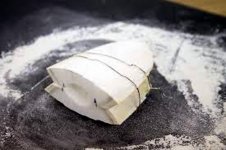
These have made for some interesting band designs...
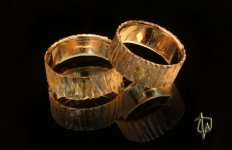
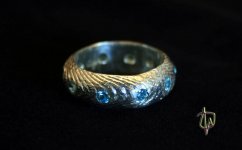
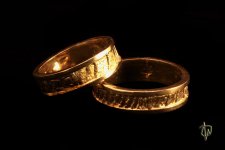
Once I get a billet made with the cuttlebone casting, I then have to form it into a ring band without damaging the natural patterns. For this pipe band, I cast the billet extra deep, to get more pronounced ridges than one would want on a ring worn on the finger. On the finger, the wearer wouldn't want it to cut into the fingers as they would use the hand, so for a pipe band, I really pushed the design, and then craved back into it to make more a fin-like design.
To keep it from looking too wonky on stummel and stem, I then cut a 1-2mm dado by hand into the briar shank and use a slight compression fit to seat the band. I've made 100's of regular bands for Skip at The Briary, and the process just has to be slow and meticulous using small files, counting strokes to get a precise dado. And, digital calipers are essential.

But, here is my new billiard with band. I managed to get the fins taller on the top of the band, giving the fins a slightly more dynamic look. And, getting a seamless join was quite tricky.
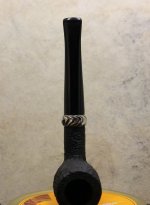

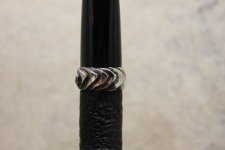
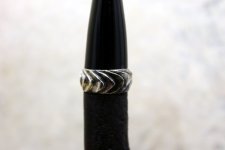
Anyways, i know that bands are like the least fascinating part of the pipe hobby, but I'm enjoying my new band. And, i thought that some here are interested in different aspects of craftsmanship, so I thought that someone might enjoying seeing and reading about the process. I've got a few more designs in mind, and maybe I can get to them soon.
I hope you've enjoyed the pics.
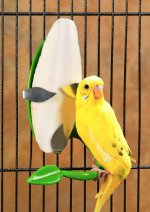
But, it is also a part of an ancient jewelry/metalsmithing process known as cuttlebone casting. There are refences to it's use in Norman and even Danish (or Northernmen) jewelry. It is very similar to casting used by Pre-Columbian sandstone processes, where the design is scratched into the soft material and then the molten metal is poured into the primitive mold. Cuttlebone has these ridges that make for a unique design on the finished piece. You cannot completely control how the finished piece will come out, so it is a bit serendipitous, or a balance between control and natural consequence.
I have made hundreds of rings using this process, and it is always a surprise how they turn out. I do have somewhat of an idea of how these will turn out, but the resulting ridges are hit or miss. But, I make a trench into the bone from the cuttlefish and then put two together to make a mold, and then pour the metal into the mold using merely gravity to fill the recesses.
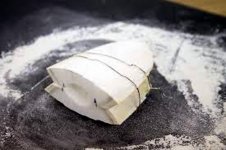
These have made for some interesting band designs...
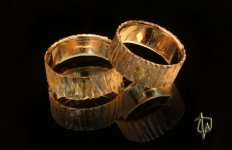
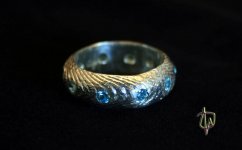
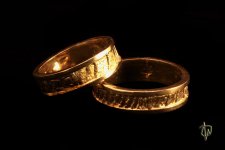
Once I get a billet made with the cuttlebone casting, I then have to form it into a ring band without damaging the natural patterns. For this pipe band, I cast the billet extra deep, to get more pronounced ridges than one would want on a ring worn on the finger. On the finger, the wearer wouldn't want it to cut into the fingers as they would use the hand, so for a pipe band, I really pushed the design, and then craved back into it to make more a fin-like design.
To keep it from looking too wonky on stummel and stem, I then cut a 1-2mm dado by hand into the briar shank and use a slight compression fit to seat the band. I've made 100's of regular bands for Skip at The Briary, and the process just has to be slow and meticulous using small files, counting strokes to get a precise dado. And, digital calipers are essential.

But, here is my new billiard with band. I managed to get the fins taller on the top of the band, giving the fins a slightly more dynamic look. And, getting a seamless join was quite tricky.
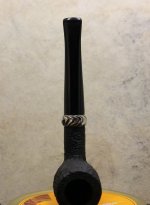

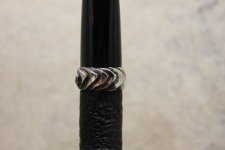
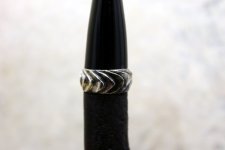
Anyways, i know that bands are like the least fascinating part of the pipe hobby, but I'm enjoying my new band. And, i thought that some here are interested in different aspects of craftsmanship, so I thought that someone might enjoying seeing and reading about the process. I've got a few more designs in mind, and maybe I can get to them soon.
I hope you've enjoyed the pics.
Last edited: