I've repaired two pipes with loose tenons/stems (that is, the tenon fit loosely in the mortise) by using a sleeve made in a 3d printer. It seems to me that this process could be useful, although it needs fine tuning.
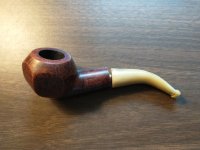
Here's the small pipe - horn stem with metal tenon - loose.
I enlarged the mortise. Then measured carefully.
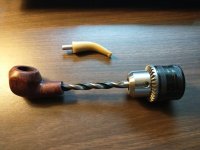
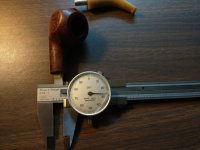
I had my son make a sleeve on his 3d printer. Here's what he said about the resin "It's a blend of UV curing resins. The brand is Siraya Tech and it's 90% 'ABS Like' and 10% 'Tenacious', blended together."
I scored the inside of the mortise to give it more surface area for the glue to adhere to, then I used superglue to glue it in. That was a mistake; I should have used a different glue. It was tricky getting the glue on the sleeve and then the glue dried too quickly. I ended not being able to push the sleeve all the way in. Even so, it went in most the way and with a bit of filing it worked.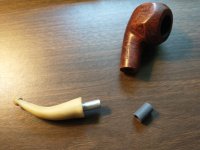
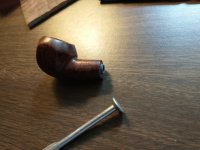
Here's how it turned out (below). A bit too tight, but I can carefully sand the new mortise.
Here's a few things I want to remember for next time:
1. Use a different, more slow-drying glue.
2. When hand drilling out the mortise, mark the bit the exact length needed so that there is no gunk-catching ridge at the bottom of the sleeve.
3. Related to 2., if there is a ridge on the bottom of the sleeve, then bevel it before inserting. Likewise bevel the top of the sleeve to make inserting the tenon easier.
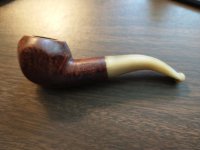
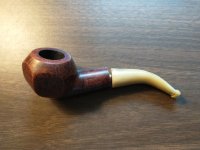
Here's the small pipe - horn stem with metal tenon - loose.
I enlarged the mortise. Then measured carefully.
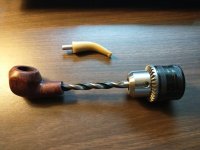
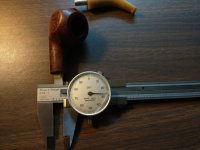
I had my son make a sleeve on his 3d printer. Here's what he said about the resin "It's a blend of UV curing resins. The brand is Siraya Tech and it's 90% 'ABS Like' and 10% 'Tenacious', blended together."
I scored the inside of the mortise to give it more surface area for the glue to adhere to, then I used superglue to glue it in. That was a mistake; I should have used a different glue. It was tricky getting the glue on the sleeve and then the glue dried too quickly. I ended not being able to push the sleeve all the way in. Even so, it went in most the way and with a bit of filing it worked.
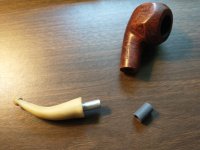
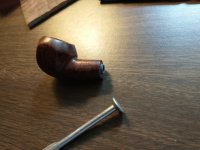
Here's how it turned out (below). A bit too tight, but I can carefully sand the new mortise.
Here's a few things I want to remember for next time:
1. Use a different, more slow-drying glue.
2. When hand drilling out the mortise, mark the bit the exact length needed so that there is no gunk-catching ridge at the bottom of the sleeve.
3. Related to 2., if there is a ridge on the bottom of the sleeve, then bevel it before inserting. Likewise bevel the top of the sleeve to make inserting the tenon easier.
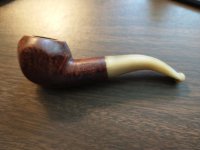
Last edited: